
Line merger
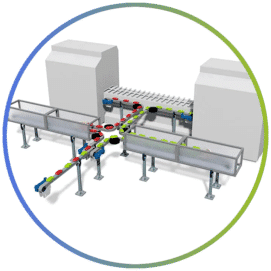
Inprosy Line Mergers (UL) allow the combination of two or more production lines or transport conveyors and delivery to a single subsequent workstation.
They have been designed to receive products from different production lines, with diverse or irregular cycles and deliver them with a regular and stable run to the next workstation.
UL devices therefore perform multiple functions: firstly they merge the flow from two or more lines or conveyors and deliver it to a single subsequent workstation; secondly, they stabilise the cycle of delivery to the next workstation in such a way that the products arrive at the required pace and separation; and thirdly, they maximise line efficiency by managing the product flow received from each line to take full advantage of the processing capacity of the next workstation.
The Line Mergers (UL) are based on the concept of Inprosy’s Dynamic Flow Regulator (DFR) and, therefore, they are also fully configurable, suitable for multiple types of products (boxes, flowpacks, bags, tubes, bottles, doypacks, machined parts, etc…) and product treatment is according to FIFO and without pressure.
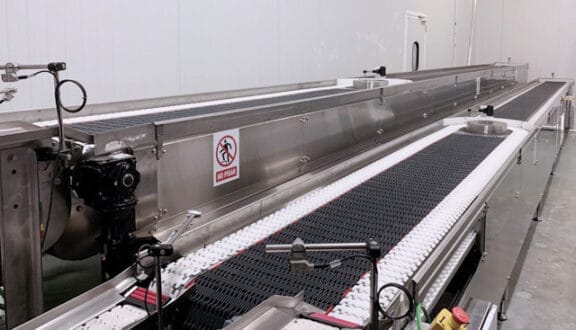
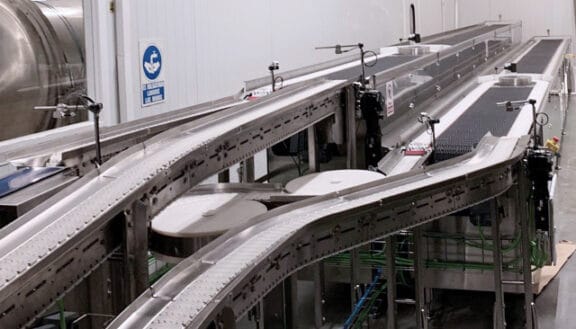
- Programmable line merging
- Based on the Dynamic Flow Regulator (DFRs) concept
- Installable at ground level and/or at height
- Feasible product sorting
- Fully configurable
- Independent product-in and product-out speeds (up to 60 m/min)
- Continuous accumulation and delivery
- Range of track shapes and sizes, up to 300 mm wide
- Size of products transported: variable according to stability and weight
- FIFO transport
- Zero-pressure accumulation
- Installation at ground level or at height
- Shape of the products transported: any from among a wide range: boxes, flowpacks, bags, tubes, bottles, doypacks, machined parts, etc…
- Entry and exit of products at the same height or at different levels
- Control software fully integrated with manufacturing line
- Stainless steel construction
- Power required: depending on the distance and characteristics of the circuit
- CE-marked
In which industries can it be used?
It can potentially be used in any industry. The limit is set by the weight and volume of the product to be transported.
What kind of products can it transport?
INPROSY solutions can transport any product below a defined maximum weight and size. For example, flowpacks, boxes, bottles, doypacks, mechanical components, canisters, electronic components…
What is the minimum size of the products to be transported?
There is no minimum size of the product to be transported. It all depends on the shape of the product and the configuration of the solution.
What is the maximum size of the products to be transported?
Depending on the shape and weight of the product, the maximum limits would be around 600x500x500 mm. For larger sizes, tailor-made solutions could be studied.
What is the minimum weight of the products to be transported?
Depending on the configuration of the solution, there would be no minimum product weight.
What is the maximum weight of the products to be transported?
Depending on the configuration of the solution, the maximum weight would be 20 kg. Tailor-made solutions could be studied for higher weights.
Is it a standard device in terms of size and capabilities, or can it be customised?
INPROSY’s range of solutions includes a line of standard products adaptable to the specific needs of each situation. In addition, INPROSY develops tailor-made solutions through its engineering department.
What is the acceptable cycle range for products to be transported?
The main factors impacting on the cycle that can be managed are the weight and shape of the product. In any case, INPROSY solutions would not be suitable for cycles resulting in conveyor speeds over 80 m/min.
Can it transport different products simultaneously?
Yes, it’s possible.
Can it connect with other devices and/or robots?
Yes, it’s possible.
Would it be modifiable in the future, if necessary?
INPROSY solutions are modular and therefore adaptable and modifiable.
What type and frequency of maintenance does it require?
INPROSY equipment is characterized by their reduced maintenance requirements.
Where can I get spare parts?
INPROSY supplies 100% of the spare parts of its solutions.
Is there technical support?
INPROSY provides technical assistance for all of its equipment.
What is the warranty period?
The warranty time of INPROSY solutions is 2 years or 4000 hours of operation.
With which interfaces is the INPROSY solutions control software compatible?
INPROSY solutions control software is compatible with most interfaces used in the industry.
Is any initial training required to operate and maintain the device?
Yes, training is included with the acquisition of any INPROSY solutions.