The effects from micro-stops to the productivity of manufacturing lines
SUMMARY: Micro-stops experienced by manufacturing lines cause a very relevant effect to their productivity.
During decades manfuacturing plants have increased their level of automation.
Nowadays it would be very difficult to conceive a new manufacturing project without a very high degree of automation.
One of the most usual automation approaches is the set-up of manufacturing or assembly lines, in which a number of workstations in succession develop all the actions needed to convert raw materials into finished products.
Manufacturing lines significantly raise productivity as they efficiently link various highly specialized workstations, focused on one or several manufacturing routines.
However, neither workstations are perfect nor are safe from risk of stops (shorter or longer). Despite machine designers have sharpened their innovation and management capacities to develop increasingly good and reliable worksations, it is not realistic to expect them to work without stops.
In a manufacturing line this risk is aggravated for two reasons:
a.- Because each stop from any of the workstations in the line can impact the manufacturing line as a whole (lacking accumulation devices or solutions),
b.- Because the fact that the manufacturing line is made of a number of workstations significantly increases the probability that any of them could experience stops.
The combined effect of all these elements to the aggregated productivity of the manufacturing line can be very important, as the resulting financial consequences to the whole business can also be.
In a theoretical simulation made with hypothetical data, the consequences arising from assembly line stops can be grasped. Let’s see an example:
Stops/Shift | Minutes/Stop | Output Actual/Theor. |
---|---|---|
0 | 2 | 100% |
1 | 2 | 97,5% |
2 | 2 | 95,0% |
3 | 2 | 92,5% |
4 | 2 | 90,0% |
5 | 2 | 87,5% |
Assumptions:
* Manufacturing line including 6 workstations.
* “Stops/Shift” = number of stops for each workstation in a 8-hour shift.
* “Output Actual/Theor.” = % of units actually produced vs. theorical.
In other words, in the most favorable scenario, where the manufacturing line experiences a single stop in each workstation during a 8-hour shift, and where this single stop lasts for only 2 minutes, the resulting impact is a reduction of 2,5% of actual line output compared to the theoretical one without stops.
If the scenario is worsened by increasing the number of stops per workstation and working shift, the erosión to manfuacturing capacity keeps raising, reaching a figure of 12,5%, when stops per machine and shift are 5.
As it is quite obvious, the impact coming from this capacity reduction can be really important, specially when the manfucaturing facility works at full capacity.
And, in all these examples, any and all stops are relevant and equally damanging. Both the planned and the unplanned stops have the same effect to the final output and productivity of the line.
Adding a Dynamic Flow Regulator (DFR) to the manufacturing line can produce a very significant mitigation of the effects of any stops experienced by the workstations located following the DFR. A DFR achieves this mitigation with the FIFO, pressureless and dynamic accumulation of the units produced by workstations located previous to the DFR in the manufacturing line. With this accumulation, “upstream” workstations can continue to produce units while the stops experienced by “downstream” worksations are resolved.
The impact of a DFR is significant:
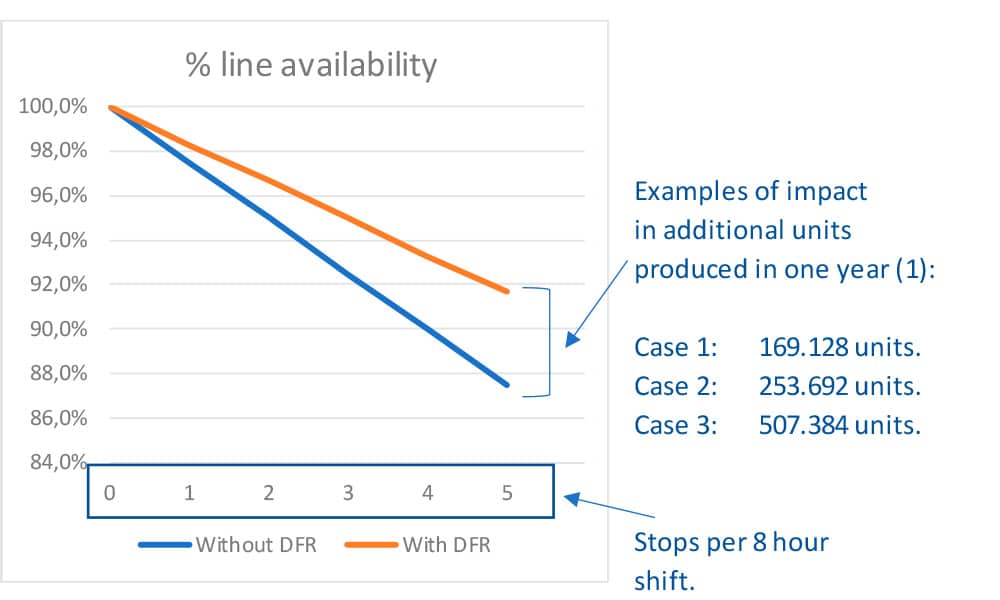
Note (1): The assumption is for lines working 3 shifts during 261 per annum, with three manufacturing cycles:
Case 1: 10 units per minute,
Case 2: 15 units per minute,
Case 3: 30 units per minute.
The conclusions of this analysis are several:
- No machine is perfect nor can it assure a 100% availability in all circumstances,
- A manufacturing line provides countless advantages. However it also suffers from the stops and failures experienced by each and all its individual workstations.
- The impact arising from short stops (both planned and unexpected) to the line productivity and output is, quite often, very high, and its visibility, low.
- One effective way to minimize this impact is to insert a Dynamic Accumulation device (for instance an Inprosy DFR series device) in the manufacturing line, as it neutralizes the effects caused by these stops, thus significantly increasing line’s productivity.